Assessment Across All Australian States and Territories
On Over 150 Facilities
Across 500 Buildings
On over 300 Unique Asset Types
10-35% STATUTORY COMPLIANCE GAPS FOUND

One of the primary functions in Facilities Management is duty of care and the management of risk and liability. What if I told you that even the most competent and well-meaning Facilities Management teams have gaps in their statutory compliance?
Between 2015 to 2017 we completed statutory compliance assessments for maintenance programmes across all Australian States and Territories on over 150 facilities across 500 plus buildings, and over 300 unique asset types. From these assessments, we found compliance gaps from 10% to 35% based on asset type and maintenance frequency.
managed risk: “reducing financial losses, improving health and safety, good will and reputation, minimising environmental and social impact, can result in reduced liabilities such as insurance premiums, fines and penalties”
We found that the main reasons for statutory compliance gaps in the maintenance regimes of these facilities was the level of commitment to technical change management processes ether in cases of establishment of new equipment, or modification and decommissioning of existing equipment as well as not keeping up to date with changes in legislation, regulations and standards over a long period of time. In a highly contracted environment like FM, we found that change management is challenging to enforce due to lack of ownership, lack of stringent project handover and operational readiness processes as well as gaps in contracted maintenance services agreements to drive change management.
We also found that compliance was more challenging for teams that operate nationally across multiple States and Territories due to increased complexities of keeping up to date across multiple legislative and regulatory frameworks.
“demonstrated compliance: transparently conforming with legal, statutory and regulatory requirements, as well as adhering to asset management standards, polices and processes, can enable demonstration of compliance;”

Outcome for the Clients
The outcome for each organisation from each of the assessment projects was that they had assurance that they were up to date and statutory compliant in their maintenance programme.
For all facilities, we provided maintenance procedures aligned with statutory requirements to fill any gaps in the organisation’s compliance. We scheduled the maintenance procedures against the assets in the asset register and provided the organisation with load up files and for their respective information systems (SAP, Archibus, Biems, Maximo, others) and assisted in the implementation of the statutory complaint maintenance procedures within their information system.

The Method for Statutory Maintenance Compliance Assurance
The method for statutory compliance assurance was to classify the asset list / register and review the current maintenance procedures against each asset class for compliance to statutory requirements. Where gaps were found, maintenance procedures were provided to address the gaps and implemented in the client information system. The process for the assessment is as follows:
Transmit Asset Register and Maintenance Procedures
We extracted the current asset list/ asset register for each facility and the current maintenance procedures undertaken.
Asset Register Validation
For facilities where there was low confidence in the asset register, a validation, condition and criticality assessment process was undertaken ether by Covaris, or by other providers with support by Covaris and Covaris tools. The validation process is outlined below.
Asset and Maintenance Procedures Data Import Into Pmsure
We imported the asset and maintenance procedures data into our proprietary software PMSure. Our software has been developed and updated over the last 15 plus years and contains a comprehensive database of legislative, regulatory, standard and codes of practice requirements for hundreds of asset types as well as preventive maintenance strategies and procedures aligned with these requirements. This database is kept up to date on a continual basis to ensure that the information is current and updated.
Asset Type Classification
We classified each facility asset list with asset types and mapped the statutory requirements for each asset type to assess gaps in compliance.
Map Statutory Requirements Against Asset Classes and Maintenance Procedures
We mapped the current facilities maintenance procedures against the asset classes and statutory requirements to assess any gaps.
Statutory Compliance Analysis
We analysed compliance based on maintenance frequency as well as maintenance tasks for the asset types against statutory requirements. The statutory requirements are defined as per the figure below.
Provided Compliant Maintenance Procedures
Were gaps were found, we provided compliant maintenance procedures to fill these gaps.
Provided Data Load up Files for Client Information System
We established data load up files based on the client information system requirements and assisted in the upload of the new maintenance procedures and maintenance schedule.

The Statutory Compliance Framework
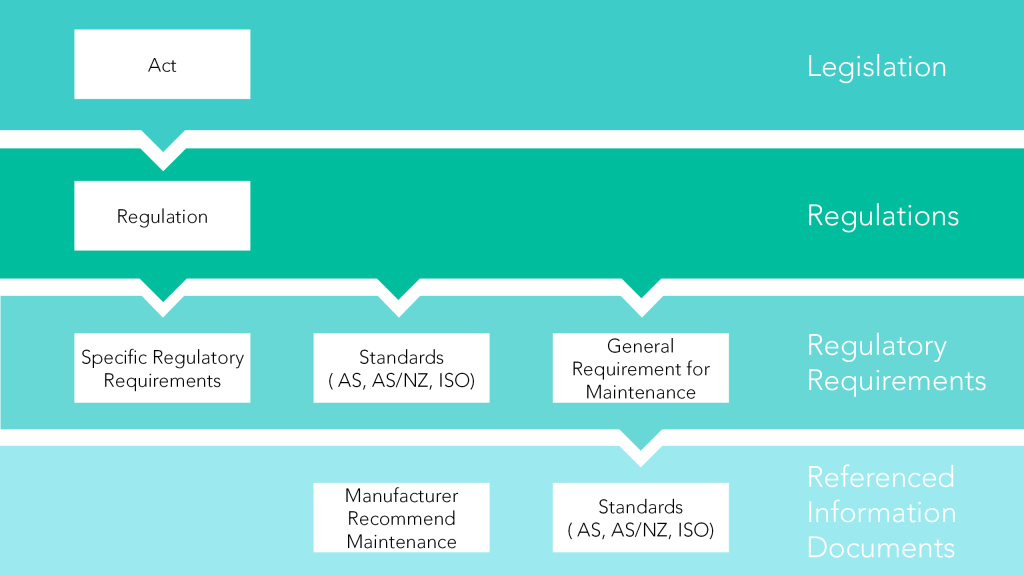
Legislation
Legislation issued by the Commonwealth Government or the State Government is consulted to determine the requirements for maintenance of the equipment types.
Compliance with the requirements of Acts is mandatory.
Regulations
Regulations are statutory rules made in accordance with an Act, which set out more prescriptive rules to establish compliance with the requirements of an Act.
It is most often the regulations, rather than the Acts, which set the specific requirements for the maintenance of equipment.
Regulations issued by the Commonwealth Government or the State Government is consulted to determine the requirements for maintenance of the equipment.
Compliance with the requirements of regulations is mandatory.
Regulatory Requirements
Applicable regulations typically require maintenance to occur either by:
- Specific maintenance or testing requirements set out in the regulations;
- Specifying compliance with an appropriate Standard; or
- Having a general requirement that maintenance occurs in accordance with manufacturer recommendations, or the recommendations of a competent person.
Where the regulations set out specific requirements for testing or maintenance, these are directly identified.
In other cases, the applicable regulations specify that compliance with an appropriate Standard is required. In these cases, the maintenance requirements of the Standards are identified.
Referenced Information Documents
Where there is a general requirement in the regulations for equipment to be maintained, but there is no specified maintenance or testing requirements, or a specific requirement for compliance with Standards, manufacturers recommendations are consulted in conjunction with other applicable codes of practice, Australian and New Zealand or International Standards.
Compliance with the requirements or recommendations on these Standards, and the recommendations set out by equipment manufacturers ensures compliance with the general maintenance requirements of the regulations.